Engine Related Notes
< Convert this web page to Palm Pilot Doc format
The car's Engine Control Unit (ECU) uses the oxygen sensor to determine how lean or
rich the car is running and adjusts the air/fuel mixture accordingly. The oxygen works in
a way similar to a battery cell. Platinum layers on the inside and outside of the probe
act as electrodes. Zirconium dioxide between the layers of platinum acts like an
electrolyte. The inside layer of platinum is exposed to the air in the engine bay, the
outer layer is exposed to the exhaust. When the O2 sensor is hot it generates positive
voltage between the two layers of platinum. Negatively charged oxygen ions in the exhaust
are attracted to the platinum and reduce the voltage created by the exhaust heat. The ECU
and air/fuel gauge reads this voltage. Thats why a rich mixture = higher voltage
from the sensor (more gas = fewer negative O2 ions to drop the voltage) . Just remember
"L=L", Lean = Low voltage. You can attach a Volt Ohm meter (black to ground, red
to the O2 sensor) to monitor your engines air/fuel ratio. Full throttle with 0.82
volts is best performance but slightly higher voltage (richer) is safer. At part throttle
the ECU will bounce the air/fuel ratio from rich to lean. You only have to worry about
full throttle. I suggest you have a copilot read the voltage while you accelerate at full
throttle. The 3 wire oxygen sensors are used to give power and ground to pre-heat the
sensor so it starts working quicker, it has no effect after the sensor gets warmed up.
Want to know more? Download o2_volts.zip, an Excel
spreadsheet with more technical data. Also, see
the O2 Sensor Replacement
How To.
Rob Robinette
A few years ago scientists discovered they could reduce the formation of nitrogen
oxides (NOx) during combustion by keeping combustion temperatures below about 2500 degrees
F. They did this by injecting an inert (non burning) gas into the air/fuel mixture of the
engine. The inert gas helps cool the combustion event to below the threshold where NOx are
formed. It turned out that exhaust gas works well as an inert gas. The EGR valve allows a
metered amount of exhaust to enter the intake of the RX-7's engine. The EGR valve uses
vacuum and an electrical signal to open the valve and inject the exhaust. The valve is
closed with no vacuum present (yes, if you remove the vacuum line from a non-California
spec car you will disable the EGR). The chart on page F-125 of the Mazda 3rg gen
Workshop
Manual shows that the EGR valve only opens under relatively light loads between 1050
and 3850 rpm. It is closed at idle, deceleration, rpm above 3850, and heavy load. So it
seems that there would be little benefit in disabling the system. The emission book,
"Understanding Automotive Emissions Control," (available at Barns and Noble)
states that an engine may need it's timing retarded and/or the air/fuel mixture richened
to prevent detonation. I've heard from several list members that have disabled the valve
with no apparent change in engine operation. See the EGR Disable How To.
Rob Robinette
The air pump reduces emissions when the engine is below 3800 rpm. Above 3800 rpm
the
main cat is hot enough without the extra air. The air pump pumps air into the exhaust and
into the main cat to give extra oxygen for the pollutants to combine with and burn. To
disable it just disconnect the gray plastic electrical connector on the top of the pump.
You wont be able to pass an emission test with it off though (you can always plug it
back in for the test). It is possible that disabling the air pump with the main catalytic
converter still installed could cause the cat to run so cool that it may get coated by
unburned oil from the oil injection pump. No one is sure about this though. See the
Air Pump Removal How To.
Rob Robinette
For a rev limiter to work on a rotary engine you have to have three of them connected,
one to each of the three coils. My Crane Hi-6 ignition amplifier has a limiter built in
and it will control the firing of the two leading plugs but the two trailing plugs are
unaffected. If the engine is under load when I hit the rev limit at 7800 rpm the rate of
rpm rise almost stops because the engine doesn't run very well when running on only the
trailing plugs. If the engine is not under load (clutch in) the rev limiter has virtually
no effect. I had to set my Crane Hi-6 to 1/2 of the desired limit--I set 3900 on the Hi-6
and the rev limiter actually takes effect at 7800 rpm. The newer H-6's may be different. I
had to set my shift light the same way, a 3600 rpm pill triggers the light at 7200
rpm.
Rob Robinette
A reading of 0 oil pressure at idle is a common problem with 3rd gen RX-7s.
The electrical connector on the pressure sending unit sits below the oil filter and it
gets dribbled on when you remove the filter (remember to make a small hole in the filter
before you remove it so it will drain). The sending unit sticks out about two inches and
is about 1 foot directly below the oil filter. Pull off the electrical wire and clean it
using steel wool or fine sandpaper. That usually does the trick.
Rob Robinette
3k Hesitation Fixes
Here's the 3000 RPM hesitation fix that I did on a couple of Chicagoland
area RX7's:
1. Put thick extra ground strap from extension manifold to firewall (use
multi-strand stereo cable, and clean metal using strong wire brush)
2. Clean the ground lug at the bottom of the motor and move it to an opening
on the engine block
3. Replace stock cat back ground with multi strand stereo cable
4. Affix a new ground point from down pipe/precat to frame (use multi-strand
stereo cable, and clean metal using strong wire brush) the key here is to put
the ground strap on the down pipe's flange, not the main cat's flange
5. Replace battery (if needed)
6. Clean fusible links. Right next to your battery's positive cable there's
a little fusible link box there (you should see a "Main 120" on it,
that's the box I'm talking about) you need to take off the cover and you should
see the positive and negative in and outs clean the contacts thoroughly with a
wire brush. This is a very important step
7. MOST IMPORTANT STEP!! Make sure your Alternator belt is tensioned to
stock specs. This is the main cause of the 3k hesitation. I would suggest buying
a new belt and make sure it's tightened using a belt tension meter (over
tightening can cause water pump failure
8. Reset your ECU by disconnecting it and pressing the brake for 5 seconds
This should work, I did this on several 93-94 RX7's. People out there think
the 3k hesitation is a voltage problem but its an AMPERAGE problem. the ECU
needs to see a consistent amount of AMPS especially during the point the
secondaries come on. The manufacturers of the 93-95 RX7s alternators
(Mitsubishi?) used cheap parts and I come to believe that the 2nd gen
alternators, although they are basically the same alternator were manufactured
better back then.
Steve
How to Find Top Dead Center (TDC)
FINDING #1 ROTOR TDC (2 rotor only)
Background:
1. The number one and number two rotors are 180 degrees apart.
2. The sparkplug hole are equidistant from the TDC
Procedures:
1. Remove both plug from the #2 (rear) rotor housing.
2. Get a mirror and light source positions that allows
looking "into" the plug hole.
3. Rotate the engine clockwise (direction of operation) via the eccentric bolt
until apex seal is positioned across the center of the #2 (rear) rotor trailing
(top)
plug hole.
4. Mark the timing wheel position at the "timing pin" which sticks out
from the front cover.
5. Again rotate the engine slowly until the same apex seal is visible across the
bottom sparkplug hole.
6. Mark the timing wheel.
7. Bisecting the arc between the two marks yield TDC (of the #1 rotor).
Functional yet Attractive,
Carlos "Spic Racer" Iglesias
http://julio.simplenet.com
Stant Radiator Cap
Fits the stock AST and AST-less thermostat housing caps. Available at most
auto parts stores. Stant # 11233, 1.1 bar (stock, post recall is 0.9
bar), better than Mazda cap in allowing proper back flow at cool down cycle.
Castrol GTX is excellent oil. But the o-rings on the oil scrapers are often far more
effective with oil made from different base stock than what Castrol uses. Oil consumption
with higher mileage engines will be lower with oil made from a different type of base
stock. One of these is Havoline. I only use Havoline 20W-50 (10W-40 also
recommended) in any rotary I work on. I am in Florida. If you are in Canada or
another cold weather territory, you may be better off with 5W-30 or 10W-30.
I use the Fram Tough Guard (no teflon) series on both my 2nd and 3rd gens. I
am using TG 3593A. The oil filter fits on both cars just fine. The 3rd gen also
uses the 6607 from Fram, but it is smaller.. so I just use the larger 3593A.
Gil Gredinger
Red Line recommends the following for the RX-7: Red Line MTL-90 (MT=Manual Transmission) goes in the transmission, 75W90 goes in the differential,
Red Line 10W40 for the engine and SI-1 in the fuel system.
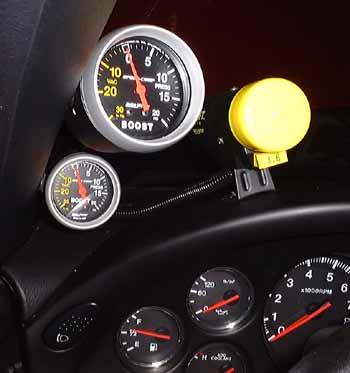
AutoMeter boost gauges -
upper 2 5/8 inch, lower 2 inch
Here are the AutoMeter options for boost gauges:
3301 - Boost-Vac./Press 30 In. Hg.Vac / 20 psi boost - 2" Face
This one is smaller but not liquid filled,
has both boost pressure and vacuum
5401 - Boost-Vac 30 In. Hg /2 0 psi - 2 5/8" Face
Larger, liquid filled version of 3301
5404 - Boost 0-35 psi - 2 5/8" Face
Similar to 5401 but only boost pressure, no
vacuum, liquid filled (this one is sweet, you don't need no stinkin' vacuum)
AutoMeter makes a single and twin stick-on pod for the 3rd gen A pillar that fits 2
inch gauges. Call Jeg's or Summit Racing for gauges and mounts. Their p/ns are 20675
single & 20674 double. The single goes for $27 & the dual for $34.
Auto Meter Tech Support
Auto Meter has a Service/Tech dept. 815-895-8141.
To remove the power steering pump you will need a run-around loop to connect
to the steering rack where the pump used to connect. Crooked
Willow Racing sells the required loop which is ready to attach to the
steering rack for $75. You'll lose the air conditioning too unless you come up
with a pulley to replace the belt tensioner and a short v-belt to turn the A/C
pump.
Idle Speed Adjustment
850 is the correct idle speed. The lower idle speed stated
in the workshop manual only applies when you connect the TEN and GND terminals
in the diagnosis connector - in other words when you adjust the idle speed.
Connecting TEN and GND is necessary to temporarily disable the ISC (Idle Speed
Control) system. When you set the idle speed to approx. 725 rpm using this
method, it will jump to 850 the moment you pull the TEN-GND jumper.
-
bring engine up to normal operating temperature
-
connect TEN and GND
-
connect a tachometer to diagnosis connector pin IG- and a chassis ground
-
make sure the wax rod operated lever completely separates from the fast
idle cam
-
adjust idle speed to approx. 725 rpm by turning the idle speed
adjusting screw located UNDER the throttle body between the two 10mm cap nuts that attach the charge air pipe to the throttle body
-
if the idle speed is too high with the adjusting
screw fully screwed in
(clockwise), unlock and turn (counterclockwise) the primary throttle stop screw to give you more adjusting range for the screw under the throttle
body.
-
while adjusting idle make sure the fans are not running remove the TEN-GND jumper and verify that the ISC system takes the rpm
up to approx. 850
Bernd Kluesener
First of all, the pilot bearing and the throw-out bearing are two separate entities.
The pilot bearing is located in the rear center of the eccentric/crank shaft. Its purpose
is to keep the eccentric and tranny center lines the same, while allowing for relative
speed differences between the two. Secondly, Ive only ever heard throw-out bearings
make noise when you STEP down on the clutch. This is the only time the throw-out bearing
ever has a load on it.
As far as the transmission noise goes, if it isnt excessive, dont worry
about it...yet. In my experience all third gen manuals make some noise in neutral with the
clutch out. Dont know if this carries over to your car though. Just for comparison
sake, my old 79 Z-28 used to do the same. Its time to worry when you hear the noise
while driving. If the noise goes away in 4th gear, generally the input shaft
bearing is bad, but in some cases it can be the counter shaft bearings. If you have noise
in all gears, most likely a bearing on the main shaft (sometimes called the output shaft).
I dont know if any of this helped, but to make the story short, dont worry
about a small amount of noise while sitting in neutral. Some amount of bearing noise is to
be expected. Have you checked/changed the fluid level since you got the car? BTW,
sometimes synthetic fluid will make a tranny noisier, due to its thinner nature; just an
FYI.
Go to your local dodge dealer and have a look at the fuel pump that they use for the
viper. Its a Bosche pump that is Identical to the HKS upgrade pump. I picked one up
and put it in my car and the pump only cost me about $130. This was with a discount
though. Check it out.
Jeff Hurst
When replacing the vacuum hoses dont forget to take out the boost restrictor/pill
that is in the line between the primary turbo compressor elbow and the wastegate actuator
and install it in the new hose. This is the same line where you can install a needle valve
and use it as a manual boost controller. There is also a restrictor in the secondary turbo
pre-control line. See Boost
controller for instructions and the Hose Diagram.
If you remove the stock air box you will hear both of these valves dumping air. The
charge relief valve dumps boost from the secondary turbo between 3000 and 4500 rpm. This
is during the pre-spin stage of the turbo. While this is happening, the turbo control door
is closed, the pre-control door is open (allowing exhaust to pre-spin the turbo), and the
charge control door is closed, keeping the primary turbo isolated.
You should hear the CRV at these rpm; what youre hearing *the moment* you
let off the gas is the Air Bypass Valve (the stock blow-off valve). This can be replaced
with an after market blow-off valve. It isnt computer-controlled, but simply driven
by the pressure/vacuum within the intake extension manifold. The stock blow-off valve is a
good unit and doesn't need to be upgraded.
If you disconnect the charge relief valve, your secondary turbo wont be pre-spun
at 4500 when it comes online, creating additional turbo lag.
I have done it. With the help of a few listers, lots and lots of patience, lots of
tools, a good torque wrench, and extra hands. It takes about 5-6 hours to take it out,
less the second time. I figure I could do it now in about 3 hours. Putting it back
together takes much longer though. NOTHING about it is impossible. Its actually not bad at
all, but it's tedious. The shop manual describes everything you need to
do in good detail. Everything must come out of the passenger side of the engine bay.
Intake, y-pipe, EGR, even the heat shield for the abs needs to be moved a bit.
pre-cat
(replace it with a down-pipe immediately) and a ton of hoses. If you have thin fingers,
this isn't impossible. If you have thick pudgy hands, dont even try, it will be impossible
in some parts (unfortunately.) At least for a beginner it will be. Get someone with small
thin hands to get to some of the boost hoses. The rest is dooable without small hands. The
turbo assembly is heavy, you can lift it out yourself, but it requires help to put it back
in. There are lots and lots of gaskets you will need to replace. About 250 dollars worth.
You dont HAVE to replace the 2 main ones, but you only take the turbos off once.. Once the
assembly is out, send it to someplace to get it rebuilt. When it comes back, and you want
to bolt everything back up, remember how you labeled every part, where it came off, and
what order? Oh wait you didnt? BAD MOVE. Label everything. there are LOTS
AND LOTS of parts. It takes about 10 hours to put it back on, and it requires 2 people to
do it. I get to try to pull my engine this summer sometime. Anyone in the dc area with an
engine hoist and a garage I can use for about 2 weeks? :> (Engine runs fine, front
turbo is questionable, boosts fine, but blades move. Its the front cover that is bad.
Leaks oil badly. about 1500 to pull the engine and put it back in for a 2 dollar gasket.
Beat that ;>)
By skight@reliacom.com
Injector Pulse Width Staging Algorithm
The injectors on the stock [3] fuel injection system are staged (i.e. only primary
injectors followed by primary + secondary injectors). The system includes two primary
(pri) 550cc injectors and two secondary (sec) 850cc injectors, with a switchover point
from pri only to pri + sec which is a function of coolant temperature, rpm and load (to
name the main ones). At switchover, the computer notes the pulse width (pw) of the pri
injectors and reduces the pw to 39% of the pri pw, for the switchover pw of the pri + sec.
For illustration, let us assume a pri pw of 10ms when switchover occurs. Also all
calculations will be for fuel flow PER ROTOR bank of injectors. The pulse width of 10ms *
550cc(per minute) injectors = .010(sec.) / 60(sec/min) * 550(cc/min) = ** .09166.. cc's
per pulse. **
When the switchover occurs, the system stages from the pri to pri PLUS sec injectors, fuel
capacity increases to 1400cc (550 + 850) per rotor. Now the fuel flow math looks something
like this: 1400cc * 10ms * .39 (switchover correction factor) = .010(sec.) / 60(sec/min) *
1400(cc/min) * .3928 (switchover correction factor) = ** .09166.. cc's per pulse. **
Notice that both fuel flows are equal, and therefore the switchover does not interrupt the
total fuel delivery.
So why is this important? Both the Techtom-type and the "piggy-back" computer
upgrades use this algorithm at switchover, and are therefore limited by it. None of them,
as far as I can tell, have the capability to work around this mapping logic. This becomes
a problem if the injector sizes are changed, because the stock system is designed around
this critical correction factor. Make the ratio of the pri to pri + sec too large, and the
switchover results in momentary lean condition. Make the ratio to small, and the car runs
rich at staging. So the trick to increasing injector size is to maintain the ratio
of the pri (550cc) to pri + sec (1400cc) as close to .39 as possible.
And yes, this knowledge did come about through much mechanical self-flagellation, until
I installed a set of 1220cc sec to match my 850cc pri. The ratio isn't perfect
(.41) but it's the max flow within a margin of the desired ratio that I could design given
the stock injectors and fuel management system. And I DEFINITELY CAN GO THROUGH SOME GAS..
Viva Gasolina!
Carlos "Spic Racer" Iglesias
Fuel Injector Info
The 850ccs injectors are the secondary injectors. They are used under high
power/rpm conditions. The Brake Specific Fuel Consumption numbers (BSFC) for the
rotarys is 0.7. The number is the pounds per hour of fuel that it requires to make
one horsepower. So you convert from cc/min to lbs./hr and then divide your total fuel flow
by the BSFC and multiply that by the duty cycle you will use. That will give you the max
supportable horsepower your injectors can support. The baseline fuel pressure for a 3rd
gen is 40 psi with an additional pound per psi of boost which keeps the differential
across the injectors the same. BTW I use 6 x 850cc injectors on mine which comes out to
486 pp/h. Now divide this by .7 BSFC = 694.54 and multiply by duty cycle of 85% for me to
compensate for the fact that A. I will run beyond 80% and B. run at a higher pressure.
This comes out to be about 590 HP or so, which is right where I am expecting to be.
Although I should note that the .7 is probably pretty rich even for us. Consider it as a
safety margin for tuning. This is evidenced by the stock configuration only supporting 306
hp and we all know thats a little low. A number of about .6 is probably better.
Another issue is that injectors flow volume, not weight. The pounds per hour conversion
assumes a relatively light fuel where as most racing gas is more dense. Lastly this should
also explain why racing fuel helps a lot with the stock fuel system. Not only is it more
dense but also allows a lower BSFC to be used because you can run leaner without
detonation.
Kevin T. Wyum
One solution to adding more fuel to a highly modded engine
is adding additional fuel injectors and a controller. I have an older model HKS AIC. In
addition to setting the boost and rpm levels at which the additional injectors begin to
fire, it has two other controls to specify the rate of increase for fuel flow as a
function of boost and/or rpm increase. These "rate of increase" controls are
linear. That is, the "curves" are straight lines. Both curves combine as both
parameters increase. Obviously, the rpm trigger does not activate if the minimum boost has
not been reached. My old unit has an LED bar graph to show the percentage of available
fuel being used (duty cycle). It also has lights to show when each function (rpm or BOOST)
has reached the threshold. You can use this information in conjunction with your tach and
boost gauge to confirm that things are happening when you want. If I read the literature
correctly, the newer units allow you to program in these parameters directly, so it should
be easier to use. Do not, under any circumstances, rely on one of these things without
having some way of monitoring the results. A decent A/F meter is indispensable for tuning.
Without one you are flying blind. AIC's do not offer the finely tuned options of an
after-market engine management system, so even an inexpensive A/F meter can get you in the
ball park. After months of messing with mine, trying to tune it with an EGT gauge, I
installed an A/F meter. In 10 minutes, I had the system working properly. Once set up, you
can basically leave it alone. One other warning: These units do not have access to data on
coolant or ambient temperatures, so if you live in a place with wide temperature
variations, you may want to tweak the boost gain up or down a notch when the seasons
change . In other words, locate the control unit where you can get to it. Within the above
restrictions, I am very happy with my HKS unit. Once set up, it has functioned reliably
and consistently. Also, it has an interesting "test" function which fires the
added injectors full blast to verify that they are working. This extra shot of fuel can be
used to load up the exhaust with the kind of stuff which makes for spectacular flames out
the back. My exhaust system is old, but when I replace it, I will certainly experiment a
bit with the "test" button to see if I can't figure how to create a subtle
warning to those who follow too closely. Best wishes,
The anti-afterburn valve prevents backfiring as you let off the
accelerator. The high-vacuum and fuel injector lag associated with sudden throttle closure
ultimately leads to a momentarily rich A/F mixture. As a consequence, the conditions are
such that backfiring may occur. The anti-afterburn valve, which is part of the air control
valve (ACV), injects a burst of air from the air pump into the intake manifold to dilute
the overly rich intake charge. [Rob Robinette adds: This must be why backfiring seems to
increase when you disable/remove the air pump/main cat.]
Larry Mizerka
My oil analysis results are in. Performed by Cleveland
Technical Center, in Cleveland, OH. If anyone wants the phone number, send private mail.
Cost is $14.75 per sample, but you must buy a minimum of 6. Oil only had only 1450 miles
combination city/highway driving, (no track) and was taken early due to the motor being
removed and replaced.
Fuel content was less than 1% volume; water: 0%; ; solids: 0.2%; glycol: negative. The
following numbers for wear metals are in parts per million: iron: 26; chromium: 3; lead:
13; copper: 8; tin: 1; aluminum: 2; nickel, silver, and manganese: 0.
My truck ran significantly lower numbers for wear metals, with similar mileage since an
oil change: iron: 6; chromium: 0; lead: 7; copper:2; tin:4; aluminum, nickel, silver, and
manganese: 0. It also recorded less than 1% fuel by volume.
Its actually the gaps at the bottom
and sides of the radiator allowing air to escape without passing through the radiator
[that can cause overheating]. Use some black duck tape or something to seal all of the
open areas in the front mouth so that air can only pass through the radiator or IC duct. I
think all your cooling problems will go away immediately. It solved the same problem
during the One Lap.
If you want to make the same blow off valve noise between shifts that the after-market
blow-off valves do, just remove the rubber hose that goes from your air box to the factory
blow-off valve. Remember to cap the hole on the air box.
A pop-off valve is different from a blow-off valve. A pop-off valve will relieve excess
boost pressure anytime boost exceeds a pre-set level. It' used as a safety valve to keep
from over-boosting your engine. If you try to use it to control boost you will damage your
turbos by over-speeding them. A blow-off valve only releases pressure when the throttle
closes (like between shifts) when a vacuum is created in the extension manifold. That's
why the blow-off valve has a vacuum line connected to it. It's main purpose is to keep the
pressure wave that is caused when the throttle slams shut from going back and slamming
into the turbo rotor blades. The valve opens up and releases the pressure wave before it
gets back to the turbos. GReddy sells both blow-off valves and pop-off valves.
Myself and Carlos both have them setup that way and we are both very happy...very
smooth power...loose a little low end power...gain it at the top.... better over all flow
through the system...very reliable...much better boost control... almost no vacuum system
left at all...Just oil injection and boost control (I think that is all that is left)
This isnt a mod for the faint at heart...but if your running open exhaust and
want to run the big boost >>>15lbs It is a very reliable setup..
Also if your doing this mod...make sure to go ahead and grind out the waste
gate...because of the increased flow on a cool day you wont be getting less than
14-15lbs...also do some porting on the primary turbo exhaust inlet to match it to the
Secondary exhaust inlet....
By the way my turbo manifolds with only 8k miles are already have a hair line crack in
them.
My turbos have 82kmiles on them the last of which 8k miles rarely saw less than
13lbs...
HKS EVC 4 on the way....sorry PFS...purple box boost control just isnt cutting
it...fuel delivery is working like a champ though...
Sandy Linthicum Adds:
Summary of non-sequential conversion
Advantage:
Eliminates 98% of existing control system. Simple, reliable turbo control More flow,
makes higher boost for same throttle setting at upper rpm Less mechanical stress on turbo
itself when done correctly.
Disadvantages:
More exhaust noise
Significant lag UNLESS using down-pipe, center section, cat-back & intake (I.e.:
Cats must come off or remove pre-cat & use hi flow main CAT)
Significant boost starts at 3000 rpm and comes on smoothly. Stock system comes on
quicker to full boost, at lower rpm, with a jerk and make car control somewhat more
difficult.
Boost creep above 12lbs, WOT 3rd & 4th gears at greater than
5000rpm - internal waste gate mods (enlarging) can eliminate or help this problem.
Will probably void your warranty if you have one.
I prefer the smooth consistent power delivery of the non-sequential setup, especially
for the track. Boost is 5-6 lbs. at 3000 rpm and builds to your max setting by about 5000,
where (hopefully) it should stay, till redline.
Temp or quick conversion to non-sequential is easy, but I am NOT the one who can
provide you with detailed instructions. Optimum conversion would mean removing the turbo,
permanently modding it for non-sequential and reinstalling it. I would advise waiting
until it had to be rebuilt or removed for some other reason before going to this much
trouble. Of course you might be able to do all this in less time than it takes to sort out
(ongoing) the sequential system.
Non-Sequential Turbo Mod
10psi at 5000rpm at ¾ throttle :)
Heres what I did:
1. Wired turbo control door open and removed actuator rod from door mechanism.
2. Removed lines/plugged lines to charge control.
3. Removed charge relief and capped hole and vacuum line (I have since put it back on,
but didnt hook it back to the vacuum line.
4. Wastegate: Left the direct pressure line (with restrictor) in place.
Removed/capped the line that went to the solenoid.
5. Pre-control: History.
6. Installed down-pipe.
Im waiting for my A/F gauge to come in, and Ill be running to Home Depot
for the parts necessary to turn down the boost a bit, per Brooks web site.
David Liberman
In summary, RX-7 rotaries have two plugs per rotor because of the long "combustion
chamber" formed by the rotor. They are fired at slightly different times to
compensate for the rotation of the "combustion chamber" by the plugs. The
leading plug is the primary plug and the first to fire. One person that responded said
that the second spark has little actual effect on performance and that some racers had
eliminated the dual spark plug setup. Someone else said a racer they knew kept the dual
plugs but fired them simultaneously. The leading plugs fire twice as often as the trailing
because doing so allows the use of only three coils instead of four (one coil for the
leading plugs, two coils for the trailing plugs). The extra leading plug spark goes off
during the exhaust phase and has no effect. The trailing plugs contribute far more to
emissions reduction than to power production. Without functional leading ignition, power
production is around 75% of normal and idle quality is poor. Without functional trailing
ignition, on those models that do not require it for the computer to function, power is
typically reduced no more than 2% from normal. When you set your timing, you answer the
question of spark spacing. Typically, leading is 5 degrees After Top Dead Center, while
trailing is either 15 or 20 degrees ATDC, which is a 10-15 degree delay. This relationship
is not a constant. Under full throttle, the delay remains the same on pre-86
engines. Under intermediate throttle & load conditions they may actually be about the
same, depending on the model & year & operating mode of the moment. This is
totally within the control of the ECU from 86-up. The older engines use vacuum
advance control just like most old cars. However, the amount of maximum vacuum advance
used on the trailing is much larger than on the leading, so under light load there may be
very little net delay. My old rotary Suzuki had only one spark plug. It was located about
where Mazda locates the trailing plug. Idle quality was always poor, sounding about like a
car with a "full-race" cam. Power nearly disappeared above 6500 rpm, with top
speed about 106 MPH. Displacement was similar to half a 10A. Very unimpressive for a 550
lb. bike.
Check fuel pressure (fuel pump, fuel filter, fuel tank vent by removing cap),
malfunctioning double throttle and check for a plugged catalytic converter (pre-cat and
main cat).
Flooding usually happens when you run the engine for a very short time (<
2 minutes) and then shut down the car. It then won't start because excess fuel
has washed the oil from the sides of the engine and compression drops to near
zero.
If your 3rd gen has never flooded I would save this message for when it
does.
Here are the steps based on several peoples opinions and what I did that got it
running.
Assuming that the car a) will not run and b) seems to be cranking fine or maybe even a
little too well (cranks faster than normal because of low compression).
1. Pull the plugs and check for spark, if you dont know how to do this take it to
a dealer
2. If the plugs are soaked and smell like gas its flooded.
3. Pull the rest of the plugs and start them drying out or better yet get a fresh set.
4. Disconnect the battery and Pull the Fuel Pump relay, located just behind the bumper
in the engine compartment under a little black cover, its labeled.
5. Connect the battery and turn the motor over several times for about 3-5 seconds at a
time. Allow at least 30 seconds between each crank. IMPORTANT push the gas pedal to the
floor while cranking the motor. This tells the computer to NOT fire the fuel injectors.
6. Wait about ½ an hour, go read the paper check your e-mail ----- Let the car sit.
7. Repeat steps 5 and 6
8. Squirt about a tablespoon of Automatic Transmission Fluid (ATF) into each spark plug
hole.
9. Wipe up the mess you just made.
10. Put the plugs and wires back on.
11. Disconnect the battery and put the fuel pump relay back in.
12. Make sure you have enough gas, ¼ tank at least to be safe.
13. One guy mentioned putting a product called Dry Gas into the fuel tank. I dont
know if it helped or not but I did this as well, Pep Boys had it for $1.29
14. Crank the motor over once with your foot to the floor, to let the ATF get spread
around. The ATF fluid helps seal the gap between the rotors and engine cases and boosts
compression enough to start the engine.
15. Crank the motor in the normal manner and be prepared to "catch it" if it
starts to stumble. It will smoke a lot from the ATF so just let it burn the stuff off. I
ran mine till it was completely warmed up, shut it off, restarted it, and took it for a
test hop.
It started and ran well this morning. I do not know why it flooded but it sure is a
b(*&h to fix it when it does.
According to the official Mazda test procedure, boost should be as follows:
Drive to third gear with normal acceleration
Accelerate from 35 MPH at wide open throttle until passing 4500 rpm
A slight and smooth increase in power should be felt at approximately 4500 rpm
when the
second turbo comes on line. This will be about 65 MPH.
Boost should be above 10 psi up to 4500 rpm. The boost will drop to about 8 psi
just
after 4500 rpm, and will begin rising towards maximum boost (10-12 psi) depending on the
length of time the throttle is held wide open. As a benchmark, many owners were asked to
time their cars from 40 to 70 MPH in 3rd gear. To try the test yourself, simply
cruise at 35 MPH in 3rd, floor it and start a stop watch when you pass 40 and
stop it at 70. On average, a stock car should do it in about 4.9 seconds and a slightly
modified car can bring it down to the 4.2 second range.
7 psi boost usually indicates a hose blew off somewhere, whether it be a
small one that is preventing everything from functioning correctly (usually associated
with a high idle > 1000 rpm), or you have a split in one of the main pressure side
intercooler hoses. If your idle is lopey, and jumps around from ~400 -> 900, and engine
sometimes just dies on you when you come to a stop, then you most likely do have a cracked
apex seal, or stuck one. A compression test will verify this. Now if the car wont
make much power below 2500-3000 rpm, then you have major apex seal failure.
I would bet your problem is the same as mine was. I fixed it without pulling the upper
manifold as I had did the first time while replacing all hoses with silicone. The loose
hose is very difficult to see. Under the manifold there is a row of about 7 or 8
solenoids. There is one with a white connector on it. This is the solenoid that is 2nd
back from the forward side of the manifold. When I say forward I mean in referenced to
front of car. That is the Turbo Control solenoid. below the connector is a plastic port
facing the turbo side of the motor. This hose, in my best guess, has popped off or is
loose. To get to this solenoid you need move the two solenoids that are mounted next to
each other on the forward side of the upper manifold. These are the Wastegate Control and
I forget the name of the other. Unbolt these two and move them out of the way to gain
better view of the hidden Turbo Control solenoid. Take some long needle nose pliers or a
long screwdriver to poke at the hoses to see if they are loose. If in fact this hose is
loose, I would replace it completely with a silicone piece. I used a drop of glue and
tie-warps to make sure it never it comes loose again. It is a tight fit to get to but it
can be done.
I seem to be losing coolant, but cant find a leak. I ran the car for 30 minutes
and found no leaks under the car. What I did find, was that the car seems to be pushing
water into the overflow tank. I think this is my problem because I top off the levels and
after about a half hour to hour of city driving, my coolant sensor goes off, I let it sit
and find that is low on coolant. Has anybody else had this problem? Could it be a clogged
cooling system (i.e. needs a radiator flush) all help would be appreciated. 87 GXL, 114k
on car, 8K on rebuilt engine.
It could be the hose that goes from the Air Separation Tank (black plastic) to the
overflow tank (white plastic) has a leak. If it leaks then the coolant won't be sucked
back into the engine when it cools. This will cause the fluid to only flow to the tank,
never back and the tank will overflow.
Or it could be the dreaded o-ring seal failure. There is a rubber ring which encircles
the rotor chamber, sealing the sections of the motor together. The o-rings seal water out
of the combustion chambers. The problem is that these seals are exposed to heat from the
combustion process and they can fail. Once they fail, you get an unwanted path between the
cooling system and the combustion chambers. When the engine is running, combustion gasses
work their way into the cooling system creating unwanted pressure in the radiator. You can
see it as a little stream of bubbles coming out of the tube that runs into your overflow
bottle (engine warm enough for the thermostat to open). In severe cases, there is enough
unwanted pressure to blow liquid out. You may observe that the overflow tank gains liquid
as the gasses push it out, but the radiator loses it. When you shut the engine down, the
combustion chambers cool, and that pulls coolant past the o-ring and into the chamber.
This coolant comes from the radiator and not from the overflow bottle. Sometimes you will
see white smoke when you start the car. If the problem is really bad you may get a miss
until the smoke clears. This also contributes to the radiator is losing fluid. One other
check for this is to put a smog sniffer into the overflow bottle to check for the presence
of exhaust gases. Sorry to give you such bad news, but there is no cure for this one
except an engine rebuild. It seems that you recently had one. I would be interested to
know who did it, and what new parts were used.
Andrew Caldwell wrote:
check to make sure it isnt leaking
out of the water level sensor, which is a gray nut-looking thing on the front of the
thermostat housing, right above where the upper radiator hose connects. Its a
plastic part, and eventually it cracks inside and slowly leaks coolant out.
Andy you were right on the money. Once I had everything cleaned off so I could see,
there was a very fine spray coming out of the sensor. It had been seeping down on top of
the radiator hose making it appear as though that was the source.
If you hear a gurgling sound during the first 10 minutes after shutting down your 3rd
gen RX-7 you have air in the cooling system and you need to purge it. Wait till the engine
is cool, cover the radiator caps (on engine and air separation tank) with a rag, remove
them slowly and add distilled water to both radiator caps. Keep doing this each morning
before you drive the car for a few days and you finally won't be able to add any more
water and the gurgling should stop.
Rob Robinette
The Goodridge part number for the two large radiator hoses (preformed) in a kit is
GS53-B. This will get you blue ones. Allegedly a -P will get purple ones, a -Y yellow, and
a -R red ones. My call is in - awaiting answer. They are available from Summit Racing.
David Beale
12A 1.2 liter displacement engine, 1st gen Rx7 (most)
13B 1.3 liter displacement engine, GSL-SE 1st gen Rx7, all 2nd
gen, and 3rd gen (although 3rd gen is slightly different (13B REW))
20B 2.0 liter displacement engine, First 3 rotor production motor, used in Cosmo
available in Japan, New Zealand, and Australia
13J or G (I cant recall) 1.3 liter engine with 3 rotor configuration (race only,
I think you can buy one for 24,000$)
13B-MSPRE Prototype engine 1.3 Liter engine Multiple-Side Port (Both intake and exhaust
are side ported rather than Intake being side and exhaust being peripheral port) 225hp?
N/A (normally aspirated or non-turbocharged) I am saving up for the 20B after talking
to Brooks W. and his ride in Pettit's 20B monster.
Tom Walsh
I have the Blitz cat-back aluminized steel. Cant say what it weighs WRT to its
lightness. The performance very good and it sounds better than the HKS and GReddy stuff I
hear on other FDs. Better consider the stainless version as mine has started to rust
through just before the muffler canister. It also looks better than a Super Drager (IMO).
One thing, the coffee can size exhaust is pretty close to the plastic body panel (the
black part). After a track event, the heat from the exhaust melted a little off the lower
bumper.
HedgeHog
The GReddy Power Extreme has 3 1/2 inch tubing, flows straight through the muffler, and
is quieter than most other cat-backs, including the Peter Ferrel unit. It does have quite
a "rice boy" look though and because its pipes are so big they will bang against
a brace that runs over the exhaust unless your exhaust is hung just right (especially the
down pipe). I highly recommend stainless steel for all the exhaust parts. The aluminized
mild steel will rust out pretty quickly because of the rotary's high exhaust temperature.
Rob Robinette
I could not remember who posted the question on finding the model of the rotary engine,
but I found a place that normally has them in stock. He couldnt tell me if it was a
turbo model or not - But so what, if its not, just hook-up a hair dryer or
something! The place is: Hobby Warehouse, 11601 S. Cleveland Avenue, Ft. Myers, FL 33907
Telephone -(941)278-1295. He said the cost was "About $16-$17", and expected
more in later this week. Minicraft Models, Torrance, CA 90510, sells "The Visible
Mazda Rotary Engine, model kit #11201. It is a reissue of an earlier kit. I paid $20 for
it about three months ago at a local hobby shop. Check out this link. They currently sell
the model for $15.50.
Fuel Cut Boost Pressure and RPM
The ECU will cut the fuel to the rear rotor when this boost level is reached at this
rpm:
1000 rpm 11.8 psi
2000 11.8
3000 12.4
4000 13.3
5000 11.3
6000 10.7
7000 10.7
Wankel: The Curious Story Behind the Revolutionary Rotary Engine
Author: Nicholas Faith
ISBN: 0-8128-1719-2
Copyright 1975 by Nicholas Faith
Publisher: Stein and Day, Scarborough House, Briarcliff Manor, N.Y. 10510
I got this book from my local library, the Dewey decimal is 621.434
There is a list of sources from the back (no bibliography)
The Wankel Engine by Jan Norbye (Chilton Books, N.Y.)
Rotary Piston Machines by Felix Wankel (Iliffe Brooks, London)
The Wankel RC Engine (Iliffe)
"the work by the great Japanese engineer, Kenichi Yamamoto" (pub. by Toyo
Kogyo)
Wards Wankel Reports (since July 1972, Wards Communications, Inc. 28 West
Adams Street, Detroit, Michigan)
Wankel A to Z by Karl Ludvigsen
(no ISBNs given)
Emission Numbers
I hold in my hand a Maryland Emissions Inspection Certificate for a modified (down-pipe,
main cat, cat-back, PFS purple computer, IC, intake) 3rd gen:
MY RX-7 STATE
STANDARDS
Hydrocarbons: 0.27 gpm
1.25 gpm
Carbon Monoxide: 4.6 gpm
20.0 gpm
NOx:
0.0 gpm 2.5
gpm
Carbon Dioxide: 268.0 gpm
N/A
In other words, this car passed the Maryland treadmill/dyno test in flying colors.
Water Pump Failure
The water pump in the 3rd gen will fail and leak early if the belt tension is too
tight. If it's too loose it will slip and make noise. This belt must be adjusted using a
tension gauge.
Cams Advice on Hoses
I dont know if anyone is interested, but Cam at Pettit Racing told me *not*
to use the blue silicone hosing. He said that if there is any defect at the end of the
hose where you cut it, that it will begin to split quickly. He told me to use Goodyear
5/32" vacuum hosing and tie wraps. He said the 5/32" hose will fit tighter over
the fittings. Given his participation in endurance racing etc..., I think thats what
Ill do when it comes time. Note: You can avoid hose end defects by using a Craftsman
(Sears) Handicut cutting tool, it cuts very cleanly.
Ceramic Coating
Try Airborne in Oklahoma City for ceramic coatings. More than a few of us in Houston
have had positive results with their products. Sorry, I dont have their telephone
number at home where Im writing this.
Putting Power Steering Pulley on the Alternator
With the PS pulley bored out and placed on the alternator, I fixed the belt length
problem when removing the air pump and it spins the alternator slower
He quickly jotted down on a piece of paper essentially what the minimal rebuild should
consist of. Its likely that its not totally complete as the phone was ringing constantly
as he was writing it, and answering phone calls.
-
6 apex seals
-
6 apex seal springs (12 for 86+ 2mm seals)
-
1 engine gasket set
-
12 side seals
-
12 side seal springs
-
12 corner seals (I think this should be 6)
-
12 corner seal springs
-
8 oil seals
-
8 oil seal o-rings
-
8 oil seal springs (note you can substitute competition ones)
-
1 front main seal
-
1 rear main seal
-
1 thermopellet 86+
Rotary RPM
"The output shaft, and consequently the flywheel and accessory drive pulleys, are
what the tach measures for displayed rpm. The rotors are lazily turning at only 1/3 of
output shaft speed, so the main working parts of the rotary are not high rpm components,
and the combustion process is taking place at rotor speed, which is low rpm. The
combustion process of your engine at an indicated 9,000 rpm is just puttzing along at half
the speed of a piston engine turning 6,000 actual rpm."
0.82 Volts from the O2 sensor = best performance (not too lean, not too rich)
BUR7EQP (NGK 4764), BUR9EQP (NGK 5255) (P = platinum, higher # is cooler)
The original (factory) setup is to use NGK BUR9EQP in the two leading
(lower) spark plug positions and NGK BUR7EQP in the two trailing (top) spots (or
vice versa?).
Anyway, Mazda Comp confirmed that the BUR7EQP
is a hotter plug used solely to improve emissions.
For performance driving, use four NGK BUR9EQP’s to reduce the risk of
detonation. This should
apply to all 13B engines. Not sure
if the same goes for 12A’s.
Hope this helps!
Bill Del Vecchio (‘86 RX-7 GXL & ‘94 RX-7 R2)
Centerforce Dual Friction Clutch
Is recommended, also the ACT and Racing Beat Street/Strip are well liked.
|